California Company Hopes To Pave The World's Roads With Recycled Plastic
Language
Reading Level
Listen to Article
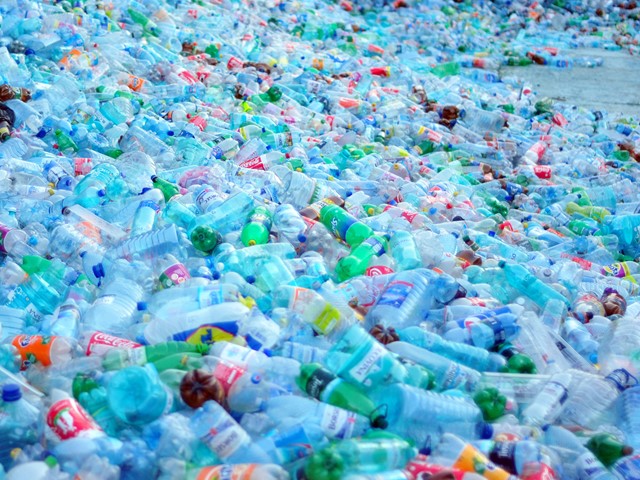
The invention of plastic has been a double-edged sword for humanity. While the cheap, versatile material has made life convenient, it is virtually indestructible and takes centuries to decompose. Since avoiding plastic is impossible, companies worldwide are coming up with innovative ways to repurpose the millions of tons of polymer waste that end up in our landfills annually. Among the latest is California-based TechniSoil Industrial, which has devised an ingenious way to reuse plastic waste to repave roads.
Road resurfacing is an expensive undertaking that starts with using special equipment to extract and grind the topmost 3-to-6 inches of asphalt. Since the recycled material is not strong enough to use on its own, half of it is discarded and replaced with fresh hot asphalt. The combined product is mixed with bitumen — a sludge-like petroleum residue that acts as a binding agent — and relaid on the surface. Repaving a single lane mile requires 42 truckloads of new material and hauling out a similar amount of unusable waste.
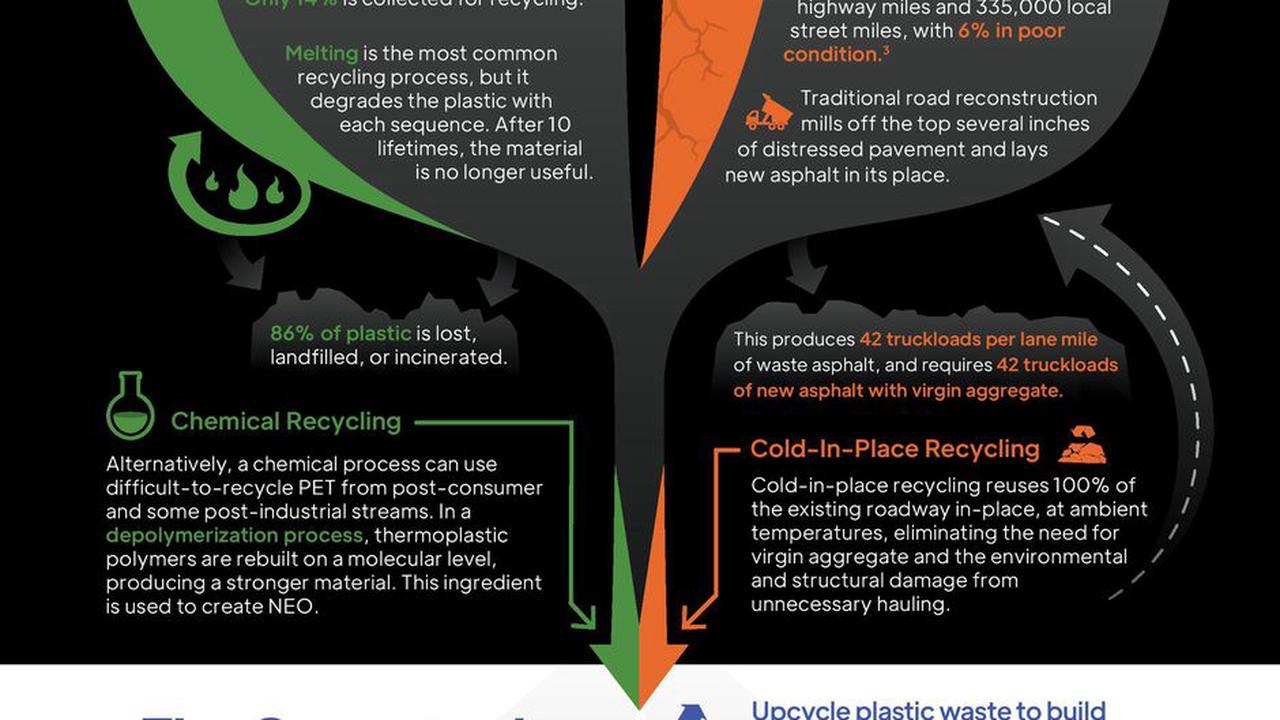
TechniSoil's process is both streamlined and sustainable. Four large construction vehicles work in unison to extract the top road layer, grind it for recycling, and mix it with the company's Neo binder — liquefied polymer made by chemically recycling discarded plastic bottles and other single-use containers. The blended product is instantly deposited back on the road, paved, and rolled over. Given that each lane mile requires the equivalent of 150,000 plastic water bottles, wide-scale implementation of the product could make a substantial difference to the world's plastic pollution.
“The advantage with recycling in place is that we avoid all of the truck traffic in and out of the construction zone,” Sean Weaver, the president of TechniSoil, says. "That eliminates the emissions from those trips and makes it faster to complete the job. We can do this work very seamlessly at night. The standard process requires heat, but the new process works cold, saving more energy."
Plastic-repaved roads are also more resistant to potholes and cracking and last about three times longer than ones resurfaced with standard asphalt, saving cities and states a substantial amount of money. “Traditional asphalt roads rely on rock for the strength of the road,” Weaver told Fast Company. “With our pavement, it relies on the matrix of a plastic binder for the strength, and the rock is simply a filler.”
Technisoil's Neo binder has proved to be extremely effective in pilot projects with the California Department of Transportation (CalTrans) and the Los Angeles Bureau of Street Services (StreetsLA). The former has already slated the eco-friendly method for repairing highways throughout the state, and StreetsLA also anticipates incorporating Neo binder in future paving projects in Los Angeles. “This is an exciting technology and a sustainable technology,” said StreetsLA Assistant Director Keith Mozee, “And it’s something that we believe going forward could be game-changing if we deploy on a large scale.”
The California company is not the first to use plastic waste to resurface roads. Dr. Rajagopalan Vasudevan, a chemistry professor in India, came up with the idea in 2001. He has since convinced officials to resurface over 9,900 miles (16,000 kilometers) of highways in his home state of Tamil Nadu with plastic waste. The technology has also been used in varying degrees on roads in the Netherlands, Indonesia, England, and South Africa.
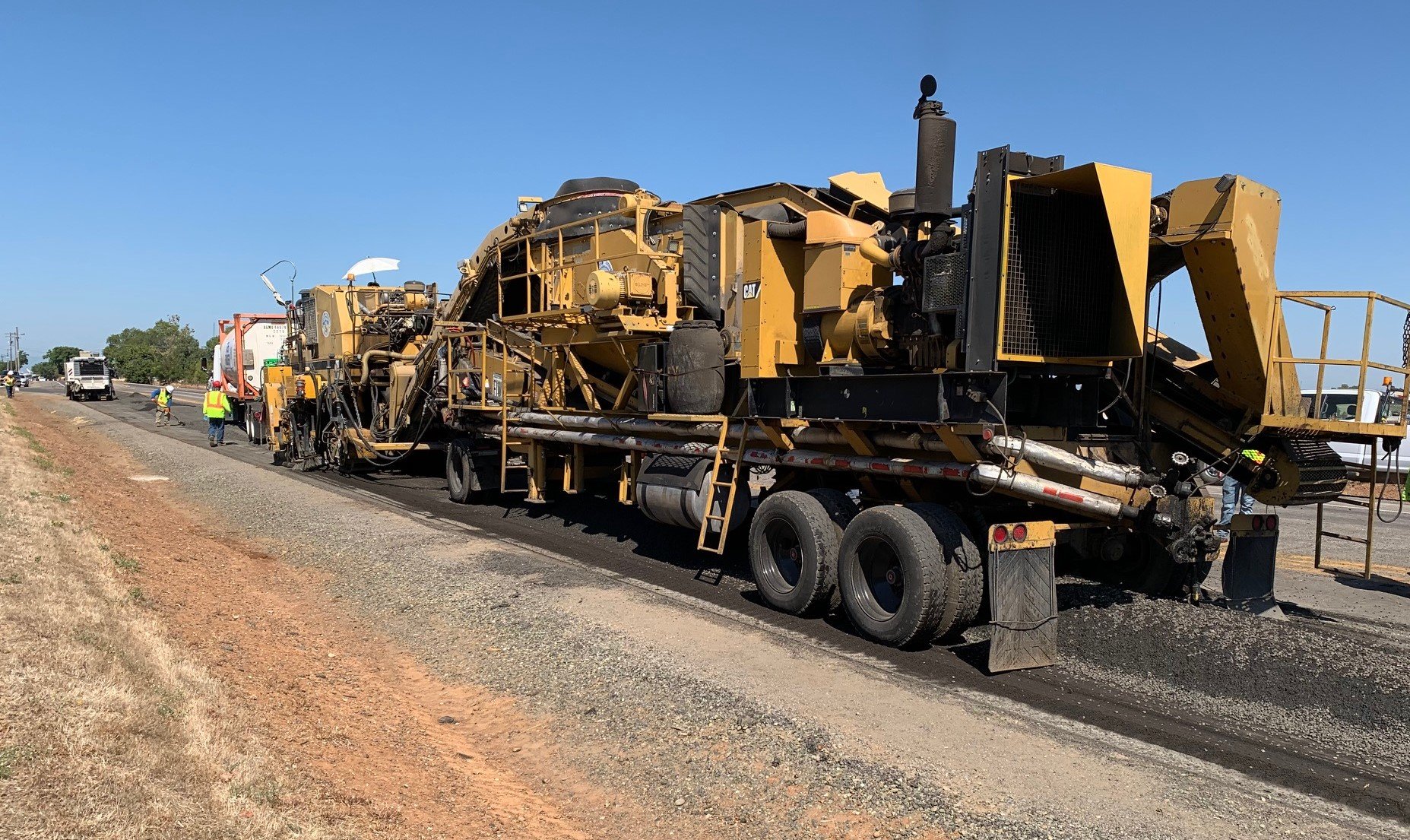
However, not everyone is convinced that plastic roads are the solution to eliminating polymer waste. Some experts assert the the toxic fumes released when plastic is liquefied could be harmful to humans. But Dr. Vasudevan maintains that since the recycled polymer only has to be heated to 338° F (170° C), no harmful substances are released. The expert says, “Plastic decomposes to release toxic fumes only if it is heated at temperatures above 518° F (270° C). So there is no question of toxic gases being released."
There is also concern that the road polymer will eventually disintegrate into microplastic particles and enter our soil and waterways. However, experts say that is unlikely since the blend of asphalt and liquefied plastic is extremely resilient to light and heat.
Weaver is undeterred by the naysayers and stongly believes that his technology may help solve the world's plastic pollution crisis. The CEO says, "We’re turning something meaningless into the single most valuable piece of infrastructure. We can consume all of the world’s waste plastic into our system, and we can do that within the next eight years."
Resources: Neopava.com, Plasticstoday.com, Cnet.com, Dailyadvent.com